Analysis of cutting phenomenon by visualization of internal stress of cutting material
Analysis of cutting phenomena by visualization of internal stress
Nagaoka University of Technology, Design and Production Engineering Group, Professor ISOBE Hiromi
Quasi-static 2D cutting phenomena has been theoretically, analytically, and experimentally verified for a long time. However, the actual machining process is dynamic, and crack initiation, especially in glass machining, is an instantaneous phenomena.
A tool dynamometer is commonly used to measure such machining conditions. It is installed between the tool rest or workpiece fixture and the machine tool to measure the machining resistance, but it does not know how the individual cutting edges and abrasive grains are generating stress and machining the workpiece.
In particular, the optimization of machining conditions for glass machining using electroplated diamond grinding wheels is largely a matter of trial and error. The reason for this is that it is not possible to determine when, how, and which abrasive grains generated defects, occurring accidentally and unpredictably, using a tool dynamometer, which can only catch the overall result of all those micro-scale dynamic phenomena.

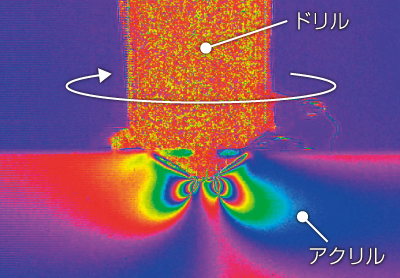
In contrast, using stress measurement with CRYSTA allowed to identify precisely individual abrasive grains and individual events real-time right on the machine. In addition, by making full use of the trigger input/output functions of CRYSTA, we succeeded in taking synchronized images of machining phenomena in the ultrasonic bandwidth.
related product
Category
- #Birefringence & stress strain measurement solutions
- #Polarization high-speed camera
- #High-speed Polarization Camera